www.engineering-suomi.com
03
'18
Written on Modified on
Teollisen tuotannonohjauksen realiteetit
Konepajat pyrkivät tuottamaan tietyn määrän tilattuja tuotteita mahdollisimman nopeasti ja kannattavasti. Tämän tavoitteen saavuttaminen edellyttää, että konepaja kykenee hallitsemaan useita erilaisia tekijöitä, kuten lastuamisparametrit, työkalukustannukset, tuotannonmuutokset, koneiden ja laitteiden käyttöaste, työkappaleiden käsittelykulut sekä materiaali- ja työvoimakustannukset.
Tuotannonohjauksella tarkoitetaan tuotannolliseen toimintaan liittyvien prosessien hallintaa tavalla, jolla saavutetaan haluttu lopputulos. Koneistusalan tuotantoprosessiin vaikuttavien tekijöiden määrä on moninkertaistunut toimialan alkuajoista. Runsaassa 200 vuodessa valmistus on siirtynyt käsi- ja pientuotannosta vakiomuotoisten tuotteiden teolliseen massatuotantoon. Valmistusmenetelmien kehittyminen sai aikaan toisen suuren muutoksen massatuotannossa: tuotantolinjojen käyttöönotto johti tuotantomäärien kasvuun ja valikoiman pienemiseen (HVLM-tuotanto). Massatuotannon kolmas merkittävä muutos oli CNC-koneiden ja robotiikan yleistyminen. Aivan viime aikoina digitaalisen tekniikan käyttöönotto ohjelmoinnissa, koneiden ja laitteiden hallinnassa ja työkappaleiden käsittelyjärjestelmissä on luonut pohjaa teollisen tuotannon neljännelle suurelle muutokselle, joka mahdollistaa kustannustehokkaan erikoistuneen tuotannon (HMLV-tuotanto).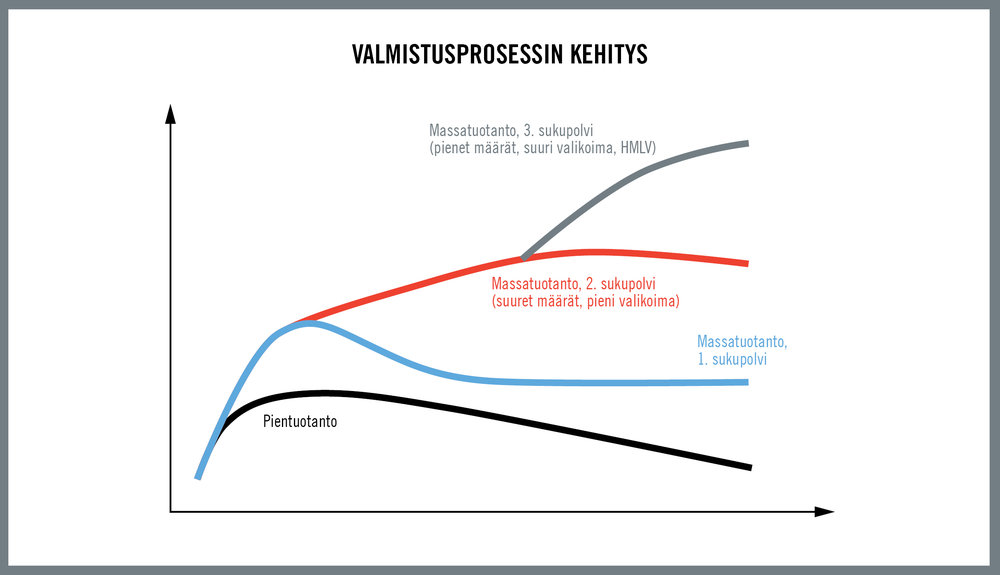
HQ_POS_Manufacturing_Process_Evolution.jpg
Tehokas siirtyminen perinteisestä massatuotannosta (HVLM) erikoistuneeseen tuotantoon (HMLV) edellyttää ennen kaikkea, että valmistuksessa tunnistetaan tuotannonohjauksen uudet ja muuttuneet vaatimukset sekä osataan hyödyntää tarjolla olevia teknologiaratkaisuja operatiivisten toimintojen analysointiin ja liiketoimintatavoitteiden saavuttamiseen. Tuottavuuden maksimoinnin kannalta on myös elintärkeää, että liian yksinkertaistetut ajattelumallit ja käytännöt hylätään ja piilevät kustannukset selvitetään.
Suuret määrät, pieni valikoima – yksinkertaista?
Vakioituja koneistusprosesseja kehitettiin 1800-luvulla, jotta voitaisiin nopeuttaa vaihtokelpoisia osia sisältävien identtisten tuotteiden tuotantoa. Autoteollisuudessa HVLM-tuotantoa hyödynnettiin tehokkaimmin, ja tuotantolinjojen käyttöönotto mahdollisti tuhansien tai jopa miljoonien samanlaisten tuotteiden vuosikausia jatkuvan valmistuksen.
Juuri HVLM-tuotannon pitkäaikaisuuden ansiosta valmistajat kykenevät saavuttamaan mahdollisimman suuren tuotantotehon, varmistamaan tasaisen laadun ja alentamaan kustannuksia hienosäätämällä prosessin eri osatekijöitä. Tuotannon vaihtelevuutta voidaan lisäksi minimoida käyttämällä erikoisteknologiaa, kuten automaattisia työkalun- ja paletinvaihtajia tai robotteja. Tuotannon oletetaan toimivan optimaalisesti, jolloin 100 % tuotantotehosta on käytössä, kustannukset voidaan ennakoida, tuotantokatkoksia ei ole, tuotteita ei hylätä laatuongelmien takia eikä uudelleentyöstöä tai purseenpoiston kaltaisia lisätoimintoja tarvita.
Yksi oletuksista on, että työkalukustannukset ovat yleensä noin kolme prosenttia tuotannon kokonaiskustannuksista. Näin saadaan kätevä laskennallinen vertailuarvo, joka valitettavasti vastaa vain harvoin todellisuutta. Työkappaleiden materiaalin koneistusominaisuudet esimerkiksi vaihtelevat: siirryttäessä teräksestä titaaniin työkalun käyttöaste voi nousta viisinkertaiseksi. Kolmen prosentin osuudesta tuleekin 15 %, mikäli muut tekijät pysyvät ennallaan.
Keskittymällä vain työkalun käyttöaikaan huomioimatta jää muita tekijöitä, kuten työkalun vaihdosta aiheutuvat seisokit. Valmistajat eivät voi sulkea silmiään työstöajan, asetusajan, työkalun ja työkappaleiden vaihtojen sekä muiden vastaavien tekijöiden vaikutuksilta koko prosessiin ja toisiinsa.
Yksinkertaistetussa esimerkissä eri prosessitekijöiden ennakoimattomasta vaikutuksesta toisiinsa konepaja valmistaa tuotetta, jonka lastuamisaika on kaksi minuuttia ja työkappaleen vaihtoaika kaksi minuuttia. Terän vaihtoon kuluu minuutti ja yhdellä terällä voidaan työstää viisi työkappaletta, joten tuotekohtainen teränvaihtoaika on 0,20 minuuttia. Jokaisen tuotteen käsittelyyn tarvitaan 4,2 minuuttia, joten tuotantoteho on noin 14 työkappaletta tunnissa. Terän yksikköhinta on 15 euroa. Tuotekohtaisen teränvaihtoajan mukaisesti 14 työkappaleen valmistukseen tarvitaan 2,8 terää (42 euroa). Konekustannus on 50 euroa tunnissa. Jos tunnissa valmistetaan 14 työkappaletta, kokonaiskustannukseksi tulee 92 euroa.
Konepaja yrittää nopeuttaa tuotantoa ja parantaa tuottavuutta lisäämällä lastuamisnopeutta 10 prosenttia. Lastuamisaika lyhenee vastaavasti 10 prosenttia (1,8 minuuttiin), mutta samalla työkalun kestoikä lyhenee lähes puoleen, jolloin yhdellä leikkuusärmällä voidaan työstää vain 2,5 työkappaletta ennen teränvaihtoa. Terän vaihtoon kuluu edelleen minuutti ja työkappaleen vaihtoon kaksi minuuttia. Yhden työkappaleen valmistukseen menee edelleen 4,2 minuuttia (1,8 minuuttia lastuamiseen, 2 minuuttia työkappaleen käsittelyyn ja 0,4 minuuttia teränvaihtoon). Tunnissa valmistuu 14 työkappaletta. Kone- ja työkalukustannukset säilyvät ennallaan, mutta tunnin tuotantoon tarvitaan nyt 5,6 terää (työkalukustannukset 84 euroa). Vaikka tuotantotehoa yritettiin parantaa, 14 työkappaleen tuotantoaika on edelleen sama, mutta kustannukset nousivat 92 eurosta 134 euroon.
Tässä esimerkissä lastuamisnopeuden lisääminen ei paranna valmistuksen tuottavuutta. Lastuamisajan muuttaminen vaikuttaa koneistusjärjestelmän muihin tekijöihin, tässä tapauksessa työkalun kestoikään ja teränvaihtoaikaan. Konepajan on siis tarkoin harkittava muutoksien vaikutukset koko prosessiin.
Piileviä kustannuksia on usein myös prosessin eri vaiheisiin varatuissa ajoissa. Monissa konepajoissa esimerkiksi kääntöterien vaihtoon on varattu aikaa yksi minuutti. Todellisuudessa kuitenkin vaihtoon voi kulua 2–10 minuuttia, mikä tarkoittaa 60–600 sekunnin eroa suunniteltuun aikaan.
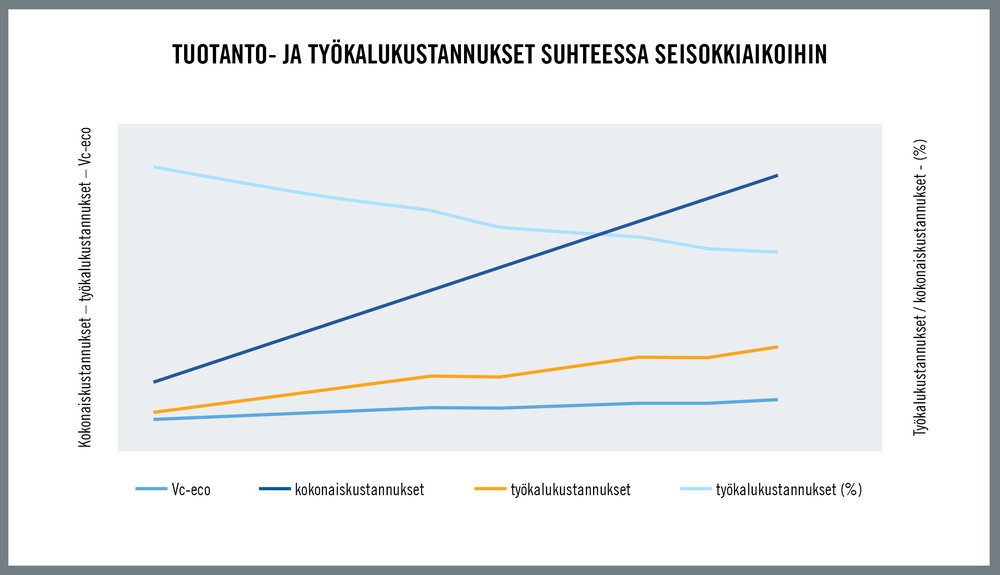
HQ_ILL_Production_Cost_And_Tooling_As_A_Function_Of_Increasing_Idle_Times.jpg
Kuva 2
Erikoistuneen tuotannon haasteita
Nykypäivän maailmanlaajuisessa kilpailussa konepajojen on tuotettava erilaisia versioita tuotteistaan voidakseen vastata myös pienten asiakasryhmien tarpeisiin. Kehittynyt tietotekniikka mahdollistaa nopeat muutokset tuotteisiin ja koneistusohjelmiin sekä helpottaa tuoteversioiden ja varastotilanteen seurantaa. Tuotanto on siirtynyt pienien määrien erikoistuneeseen valmistukseen (HMLV), jossa voidaan käsitellä tehokkaasti alle kymmenen kappaleen tilauksia ja jopa yksittäistuotteiden koneistusta.
Pitkälle ajanjaksolle ulottuva HVLM-tuotanto mahdollistaa huolellisen suunnittelun ja prosessin eri osatekijöiden hienosäädön. Tietokoneistettu suunnittelu ja varastonohjausjärjestelmät tukevat tuotetyypin ja tuotantomäärän nopeaakin muuttamista, mutta juuri tämä tekee HMLV-tuotannon suunnittelusta monimutkaista ja reaktiivista. Kymmenen kappaleen tilausta saattaa seurata vaikkapa yhden osan työstöä edellyttävä jatkotilaus. Työkappaleen materiaali voi muuttua teräksestä alumiiniin tai titaaniin ja tuotteen rakenteeseen voidaan tehdä monimutkaisia lisäyksiä. Työkalun kestoikää ei yleensä ole aikaa testata koekappaleilla.
HMLV-tuotannossa työkalun kestoikä on yleensä vain arvioitava ja varmuuden vuoksi työntekijä vaihtaa työkalun arvioidun ajan kuluttua, vaikka se ei vielä olisikaan saavuttanut todellista kestoikäänsä. Lastuamisaika on vain yksi monista prosessin osatekijöistä. HMLV-tuotannossa työkappaleiden ja kiinnittimien käsittelyyn sekä työkalujen ja kääntöterien vaihtoon kuluu usein enemmän aikaa kuin varsinaiseen lastuamiseen. Työkalujen käsittelyyn, työstökoneen käyttöön, seisokkiaikaan sekä välittömiin työvoima- ja materiaalikustannuksiin voi liittyä piileviä kustannuksia. Nykyaikaisessa tuotannonohjauksessa onkin huomioitava työkalukustannukset, työkappaleen materiaalikustannukset, laite- ja tuotantokustannukset, seisokkiajan laitekustannukset sekä palkkakulut ja ylläpitokustannukset.
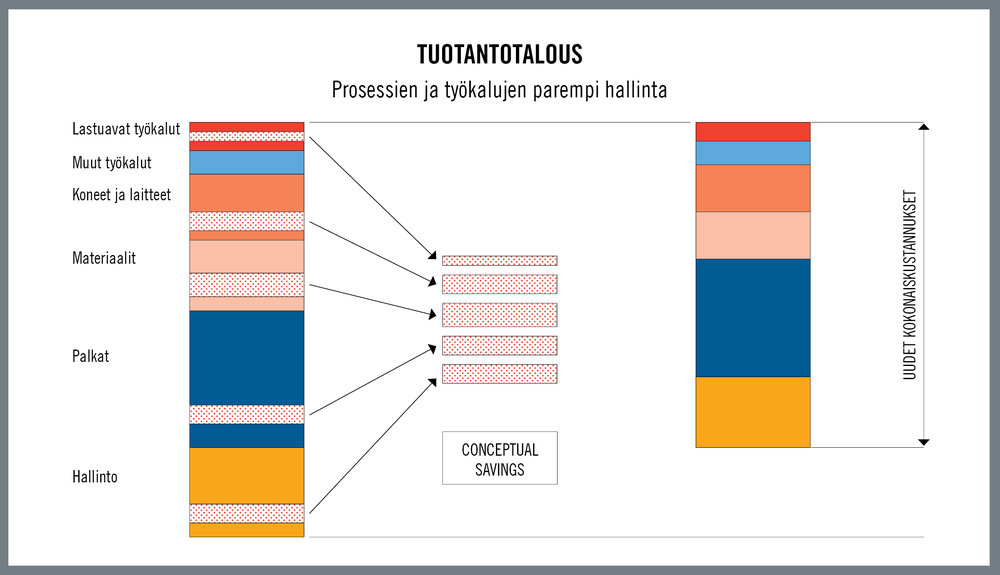
HQ_ILL_Production_Economics
Kuva 3
HMLV-tuotannon nopeasti muuttuvat tuotevaatimukset vaikeuttavat huippuluokan tuotantotehon saavuttamista. Pitkän aikavälin HVLM-tuotannossa koekappaleiden ja säätöjen avulla voidaan saavuttaa yli 90 prosentin teholukuja. Toisaalta, jos yksittäinen tuote onnistutaan valmistamaan 100 prosentin teholla, mutta tuote on hylättävä tai työkappale vioittuu, tuotantoteho on käytännössä nolla. Laatua, kustannuksia ja tuotantoaikaa koskevat vaatimukset pysyvät ennallaan, mutta yksittäisen työstön tehokkuudesta tulee ensisijainen kriteeri. Työkalun rikkoutumisen välttäminen on todennäköisesti tärkein huomioitavista tekijöistä. Etuna lyhyissä tuotantosarjoissa on, että työkalun kulumista ei tarvitse ottaa huomioon, joten konepaja voi perustellusti käyttää aggressiivisempia ja tuottavampia lastuamisparametreja.
Vastaavanlainen muuttuja on terän vaihtaminen tai kääntäminen. Jos odotetaan liian kauan, työkalu voi rikkoutua ja tuotanto keskeytyy tai työkappale vaurioituu. Jos työkalu vaihdetaan tai käännetään liian usein, työkalukustannukset kasvavat ja koneistuksen keskeytykset lyhentävät tehokasta tuotantoaikaa. Teränvaihtoprotokollaa suunniteltaessa on huomioitava sen vaikutukset koko koneistusjärjestelmään, ja protokollaa on noudatettava kurinalaisesti.
Yhteenveto
Lastuamisjärjestelmän eri osatekijöiden väliset suhteet ovat usein monimutkaisia. Lastuamisolosuhteiden, työkappaleen materiaalin tai tuotemäärän muuttaminen vaikuttaa työkalun kestoiän lisäksi moniin muihin lastuamisjärjestelmän osiin. Tuotannonohjauksessa nämä kaikki osatekijät on huomioitava, jotta niiden väliset suhteet muodostavat toimivan kokonaisuuden. Jokainen konepajan työntekijä ei voi kuitenkaan olla huippumatemaatikko eikä työntekijöillä yleensä myöskään ole aikaa koko järjestelmän toiminnan pohtimiseen. Tarjolla onkin eri palveluntarjoajien tuotantoanalyysi- ja hallintapalveluita (katso kainalojuttu), jotka antavat valmistajille kattavan kuvan tuotantoprosessista sekä ohjeita tuottavuuden maksimointiin ja toimintojen optimointiin.
Konepajojen omistajat kertovat usein miten heidän tilauskantansa on riittävä ja asiakkaansa maksukykyisiä, mutta toiminta ei silti ole kannattavaa. Ratkaisu tähän ongelmaan on nykyaikaisen tuotannonohjauksen reaaliteettien tunnistamisen lisäksi laiminlyötyjen tai
piilevien kustannuksien selvittäminen, jotta valmistustoiminnasta saadaan mahdollisimman tuottavaa.
Sidebar
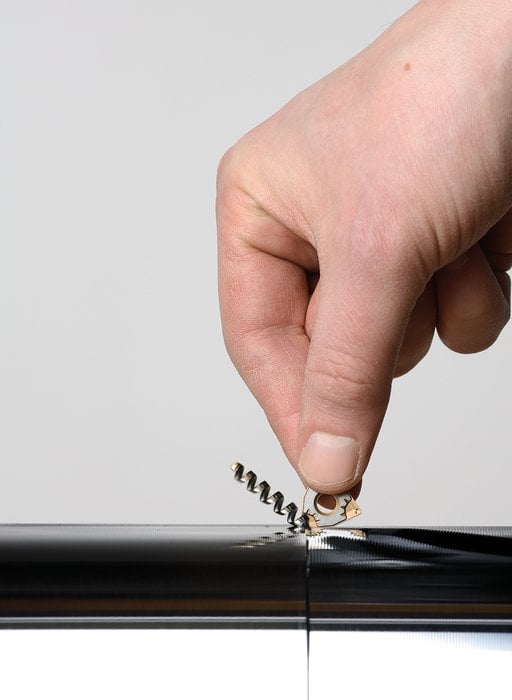
HQ_IMG_Duratomic_Chip.jpg
Kuva 4
Automatisoitu analyysi
Massatuotannon alkuajoihin verrattuna valmistuksen tuottavuuteen ja kustannuksiin liittyvien osatekijöiden määrä on moninkertaistunut. Koneistukseen liittyvien toimintojen ja laitteiden kehittyessä myös tuotantojärjestelmän eri osien väliset suhteet ovat tulleet entistä monimutkaisemmiksi. Eri osatekijät vaikuttavat toisiinsa, esimerkkinä vaikkapa tuotantomäärän muuttaminen, joka vaikuttaa työkalujen ja laitteiden käsittelyyn sekä ylläpito-, työvoima- ja yleiskustannuksiin.
Suurimpana haasteena on eri tekijöiden ja niiden välisten monimutkaisten suhteiden selvittäminen, mikä edellyttää valmistusprosessien systemaattista mittausta, valvontaa ja hallintaa.
Seco Toolsin tuottavuus- ja kustannusanalyysijärjestelmä (PCA) tarkastelee kattavasti koko valmistusprosessia ja pyrkii löytämään keinot kustannuksien vähentämiseen ja tuottavuuden parantamiseen. Järjestelmä perustuu Seco Toolsin vuosikymmenien kokemukseen tuotantoyrityksien toiminnasta eri puolilla maailmaa. Seco Tools yhdistää osaamisensa pitkälle kehitettyihin tietokoneanalyyseihin ja -algoritmeihin, kuten Monte Carlo -simulointi, joka mahdollistaa kustannusmallien automatisoinnin.
Valtuutettu Seco Toolsin edustaja suorittaa PCA-analyysin, jossa arvioidaan kaikki tuotantoprosessiin liittyvät työkalut ja teknologiat. Analyysin perusteella luodaan kattava raportti, joka käsittää sekä prosessitiedot (kuten työkalu- ja lastuamisarvot) että kustannustiedot (kuten osakohtaiset kustannukset, tuotantomäärä tunnissa ja sijoituskustannukset). PCA-analyysissä voidaan arvioida tuotantolaitoksen koko toiminta, mukaan lukien yksittäisen koneen käyttö ja työkappaleen kaikki valmistusvaiheet.
Analyysin ytimessä ovat tuottavuuden parannukset, joilla on suurin vaikutus kustannuksiin. Järjestelmä huomioi pullonkaulat ja operatiiviset rajoitukset sekä tunnistaa kohteet, joita tulee tarkastella lähemmin.
PCA-analyysi aloitetaan vertaamalla kohteena olevan valmistustoiminnan tuotantoaikoja ja -kustannuksia muihin vastaaviin tuotantolaitoksiin. Tässä vaiheessa PCA-järjestelmä tarkastelee työkaluihin liittyviä tekijöitä, kuten prosessiparametreja, työkiertoaikoja ja tehovaatimuksia. Toisessa vaiheessa järjestelmä arvioi valmistusprosessia muuttamalla lastuamisolosuhteita ja käytettäviä työkaluja. Kolmannessa vaiheessa voidaan muuttaa varsinaista prosessia yhdistämällä toimintoja ja tutkimalla suurempia muutoksia, kuten koneistustyökalujen päivityksiä.
Seco Toolsin PCA-analyysia käyttäjät konepajat säästävät keskimäärin jopa 30 %, ja heidän tuottavuutensa kasvaa jopa 40 % teollisuuden sektorista riippumatta.
Tekijä:
Patrick de Vos, Seco Tools Groupin teknisestä koulutuksesta vastaava johtaja